آزمونهای غیر مخرب ( Non Destructive Testing)
- مجموعه: مقالات مهندسي > مهندسي مكانيك | کلمات کلیدی : آزمونهای+غیر+مخرب+(+Non+Destructive+Testing)+
آزمونهای غیر مخرب ( Non Destructive Testing)
آزمونهای غیر مخرب ( Non Destructive Testing)
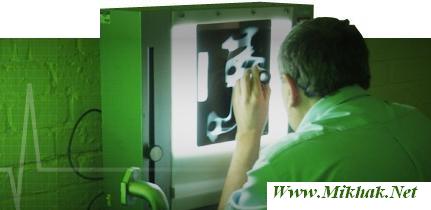
مهندسین معمولاً عادت دارند خواص یك ماده را روی نمونههای مخصوصی كه از همین ماده تهیه شدهاند با آزمونهای استاندارد ارزیابی كنند. اطلاعات بسیار ارزشمندی از این آزمونهای به دست میآید كه شامل خواص كششی، فشاری، برشی و ضربهای ماده مورد نظر است. اما این آزمونها ماهیت تخریبی دارند. بعلاوه خواص ماده به گونهای كه با آزمونهای استاندارد تا حد تخریب تعیین میشود، به یقین راهنمای روشنی در مورد مشخصات كارایی قطعهای نیست كه بخش پیچیدهای از یك مجموعه مهندسی را تشكیل میدهد.
در طی تولید و حمل و نقل امكان دارد كه انواع عیوب با اندازههای مختلف در ماده یا قطعه به وجود آیند. ماهیت و اندازه دقیق هر عیب روی عملیات بعدی آن قطعه تاثیر خواهد داشت. عیوب دیگری نیز مانند تركهای حاصل از خستگی یا خوردگی ممكن است در طی كار قطعه ایجاد شوند. بنابراین برای آشكار سازی وجود عیبها در مرحله تولید و نیز جهت تشخیص و تعیین سرعت رشد این نقصها در طول عمر قطعه یا دستگاه ، داشتن وسائل مطمئن ضروری است.
منشا بعضی عیوب كه در مواد و قطعات یافت میشوند، عبارتند از:
– عیوبی كه ممكن است طی ساخت مواد خام یا تولید قطعات ریختگی به وجود آیند (ناخالصیهای سرباره، حفرههای گازی، حفرههای انقباضی، تركهای تنشی و … )
– عیوبی كه ممكن است طی تولید قطعات به وجود آیند (عیوب ماشینكاری، عیوب عملیات حرارتی، عیوب جوشكاری، تركهای ناشی از تنشهای پسماند و …)
– عیوبی كه ممكن است طی مونتاژ قطعات به وجود آیند (كم شدن قطعات، مونتاژ نادرست، تركهای ناشی از تنش اضافی و …)
– عیوبی كه در مدت كاربری و حمل و نقل به وجود میآیند (خستگی، خوردگی، سایش، خزش، ناپایداری حرارتی و …)
روشهای مختلف آزمونهای غیرمخرب در عمل میتوانند به راههای بسیار متفاوتی در عیب یابی به كار روند. اعتبار هر روش آزمون غیرمخرب سنجشی از كارایی آن روش در رابطه با آشكارسازی نوع و شكل و اندازه بخصوص عیبها است. بعد از آن كه بازرسی تكمیل شد، احتمال معینی وجود دارد كه یك قطعه عاری از یك نوع عیب با شكل و اندازه بخصوص باشد. هر قدر این احتمال بالاتر باشد اعتبار روش به كار رفته بیشتر خواهد بود. اما باید این واقعیت را به خاطر داشت كه بازرسیهای غیرمخرب برای اغلب قطعات به وسیله انسان انجام میگیرد و در اصل دو نفر همیشه نمیتوانند یك كار تكراری مشابه را بطور دقیق همانند یكدیگر انجام دهند. از این رو باید یك ضریب عدم یقین در برآورد اعتبار بازرسی به حساب آورده شود و ارزش تصمیماتی رد و یا قبول قطعه باید از رویدادهای آماری تخمین زده شود.
نقش بازرسی غیرمخرب این است كه با میزان اطمینان معینی ضمانت نماید كه در زمان بكارگیری قطعه برای بار طراحی، تركهایی به اندازه بحرانی شكست در قطعه وجود ندارند. همچنین ممكن است لازم باشد كه با اطمینان، عدم وجود تركهای كوچكتر از حد بحرانی را نیز ضمانت كند. اما رشد تركهای كوچكتر از حد بحرانی. بویژه در مورد قطعاتی كه در معرض بارهای خستگی قرار دارند و یا در محیطهای خورنده كار میكنند، اهمیت دارد، بطوریكه این گونه قطعات، قبل از این كه شكست ناگهانی در آنها اتفاق بیفتد، به یك حداقل عمر كار مفید برسند. در برخی حالتها، بازرسیهای مرتب و متناوب جهت اطمینان از نرسیدن تركها به اندازه بحرانی ممكن است ضروری باشد.
بكارگیری ایدههای مكانیك شكست در طراحی، برای توانایی روشهای مختلف آزمونهای غیرمخرب در آشكارسازی تركهای كوچك، حد و مرز تعیین میكند. اختلاف بین كوچكترین ترك قابل آشكارسازی و اندازه بحرانی آن، میزان ایمنی یك قطعه است.
در هر برنامه خاص بازرسی، تعداد عیوب شناسایی شده (هر چند زیاد)، با تعداد واقعی آنها مطابقت پیدا نمیكند، بنابراین احتمال شناسایی یك قطعه سالم و بدون عیبهای با اندازههای گوناگون كاهش مییابد. اما هنگامی كه قطعات بسیار مهم مورد نظر هستند، سعی بر این است تا حد امكان عیبهای بیشتری شناسایی شوند و تمایل به قبول تمام نشانههای وجود عیبها زیاد است.
زیرا اگر قطعهای در طی بازرسی مردود و غیرقابل مصرف معرفی شود، بهتر از آن است كه هنگام استفاده منجر به شكست فاجعه آمیز شود. مسلم است مهندسی كه ایدههای مكانیك شكست را مورد استفاده قرار میدهد، علاقهمند است كه بداند به چه اندازه عیبها را در هنگام بازرسی مورد نظر داشته باشد. انتخاب روش با این بررسی اولیه تعیین میشود و تمام پارامترهای دیگر در درجه دوم اهمیت قرار میگیرند. برای مثال بازرسی تركهای مربوط به خستگی قطعات فولادی به روش فراصوتی كه نسبتاً براحتی قابل اجرا است، در مقابل تجزیه و تحلیل به روش جریان گردابی برای آشكارسازی تركهایی به طول 5/1 میلیمتر، كنار گذاشته میشود زیرا احتمال آشكارسازی این تركها با فراصوتی 50 درصد و با جریان گردابی 80 درصد است.
یكی از فایدههای بدیهی و روشن به كار بردن صحیح آزمونهای غیرمخرب، شناسایی عیوبی است كه اگر بدون تشخیص در قطعه باقی بمانند، موجب شكست فاجعه آمیز قطعه و در نتیجه بروز خسارتهای مالی و جانی فراوان خواهند شد. استفاده از این روشهای آزمون میتواند فواید زیادی از این بابت ، در بر داشته باشد.
بكارگیری هر یك از سیستمهای بازرسی متحمل هزینه است، اما اغلب استفاده موثر از روشهای بازرسی مناسب موجب صرفهجوییهای مالی قابل ملاحظهای خواهد شد. نه فقط نوع بازرسی، بلكه مراحل بكارگیری آن نیز مهم است. بكارگیری روشهای آزمون غیرمخرب روی قطعات ریختگی و آهنگری كوچك بعد از آنكه كلیه عملیات ماشینكاری روی آنها انجام گرفت، معمولا بیهوده خواهد بود. در اینگونه موارد باید قبل از انجام عملیات ماشینكاری پرهزینه قطعات بدقت بازرسی شوند و قطعاتی كه دارای عیوب غیرقابل قبول هستند، كنار گذاشته شوند. باید توجه داشت كلیه معایبی كه در این مرحله تشخیص داده میشوند، نمیتوانند موجب مردود شدن قطعه از نظر بازرسی باشند. ممكن است قطعهای دارای ناپیوستگیها و تركهای سطحی بسیار ریز باشد كه در مراحل ماشینكاری از بین بروند.
آزمایش پرتو نگاری و تفسیر فیلم Radiographic Testing and Film Interpretation
تابش الكترومغناطیسی با طول موجهای بسیار كوتاه، یعنی پرتو ایكس یا پرتو گاما از درون مواد جامد عبور میكند اما بخشی از آن، توسط محیط جذب میشود. مقدار جذب پرتو در هنگام عبور از ماده به چگالی و ضخامت ماده و همچنین ویژگیهای تابش بستگی دارد. تابش عبوری از درون ماده میتواند به وسیله یك فیلم یا كاغذ حساس آشكار شده و روی صفحه فلورسنت مشاهده شود، یا این كه توسط دستگاههای حساس الكترونیكی نشان داده شود. اگر بخواهیم دقیقتر بگوییم، عبارت پرتو نگاری به معنی فرایندی است كه در نتیجه آن ، تصویری روی فیلم ایجاد شود، بررسی این فیلم را تفسیر میگوییم.
بعد از این كه فیلم عكس گرفته شده پرتو نگاری ظاهر شد، تصویری سایه روشن با چگالی متفاوت مشاهده میشود. قسمتهایی از فیلم كه بیشترین مقدار تابش را دریافت كردهاند، سیاهتر دیده میشوند. همچنانكه پیشتر گفته شد، مقدار تابش جذب شده توسط ماده، تابعی از چگالی و ضخامت آن خواهد بود. همچنین وجود عیوب خاص، مانند حفرهها و تخلخل درون ماده، بر مقدار تابش جذب شده تاثیر خواهد گذاشت. بنابراین پرتو نگاری میتواند برای آشكار سازی انواع خاصی از عیوب در بازرسی مواد و قطعات به كار رود.
استفاده از پرتو نگاری و فرآیندههای مربوط به آن باید به شدت كنترل شود، زیرا قرار گرفتن انسان در معرض پرتو میتواند منجر به آسیب بافت بدن شود.
آزمایش فراصوتی (Ultrasonic Testing)
در این روش، امواج صوتی با بسامد 5/0 تا 20 مگاهرتز به درون قطعه فرستاده میشود. این موج پس از برخورد به سطح مقابل قطعه باز تابیده میشود. با توجه به زمان رفت و برگشت این موج، میتوان ضخامت قطعه را تعیین كرد. حال اگر یك عیب در مسیر رفت و برگشت موج باشد، از این محل هم موجی بازتابیده خواهد شد كه اختلاف زمانی نسبت به مرحله اول، محل عیب را مشخص میكند.
روشهای فراصوتی به طور گستردهای برای آشكارسازی عیوب داخلی مواد به كار میروند ولی میتوان از آنها برای آشكارسازی تركهای كوچك سطحی نیز استفاده كرد.
بازرسی با ذرات مغناطیسی (Magnetic Particle Testing)
بازرسی با ذرات مغناطیسی، روش حساسی برای ردیابی عیوب سطحی و برخی نقصهای زیر سطحی قطعات فرو مغناطیسی است. پارامترهای اساسی فرآیند به مفاهیم نسبتاً سادهای بستگی دارد. هنگامی كه یك قطعه فرومغناطیسی، مغناطیس میشود، ناپیوستگی مغناطیسی كه تقریباً در راستای عمود بر جهت میدان مغناطیسی واقع است، موجب ایجاد یك میدان نشتی قوی میشود. این میدان نشتی در رو و بالای سطح قطعه مغناطیس شده حضور داشته و میتواند آشكارا توسط ذرات ریز مغناطیسی دیدپذیر شود. پاشیدن ذرات خشك یا ذرات مرطوب با یك مایع محلول بر روی سطح قطعه، موجب تجمع ذرات مغناطیسی روی خط گسل خواهد شد. بنابراین پل مغناطیسی تشكیل شده، موقعیت، اندازه و شكل ناپیوستگی را نشان میدهد.
یك قطعه را میتوان با به كاربردن آهنرباهای دائم، آهنرباهای الكتریكی و یا عبور یك جریان قوی از درون یا برون قطعه، مغناطیس كرد. با توجه به این كه با روش آخر میتوان میدانهای مغناطیسی با شدت زیاد در داخل قطعه ایجاد كرد، این روش به صورت گستردهای در كنترل كیفی محصول به كار میرود زیرا این روش حساسیت خوبی برای شناسایی عیوب قطعات و آشكارسازی آنها عرضه میدارد
بازرسی با مایعات نافذ ( Liquid Penetrant Testing)
بازرسی با مایعات نافذ یكی از روشهایی است كه میتواند برای عیب یابی تعداد وسیعی از قطعات مورد استفاده قرار گیرد، به شرطی كه عیبها به صورت ترك در سطح قطعه ظاهر شوند. اساس روش بر این است كه مایع نافذ بر اثر جاذبه مویینگی به درون تركهای سطحی نفوذ كرده و پس از یك مرحله ظهور، هر عیبی كه به شكل ترك یا شكستگی در سطح قطعه وجود دارد، با چشم رویت میشود. برای بهتر دیده شدن این تركها، مایع نافذ معمولاً به رنگهای روشن و قابل دید بوده و یا به ماده فلورسنت آغشته میشود. در حالت اول معمولاً برای رنگین نمودن مایع از رنگ قرمز استفاده میشود كه با نور روز یا نور مصنوعی قابل دید باشد، ولی در حالت دوم برای دیدن تركها و درزها باید از نور فرابنفش استفاده شود.
امروزه، بازرسی با مایع نافذ، یكی از مهمترین روشهای صنعتی است كه برای مشخص نمودن انواع مختلف عیبهای سطحی مواد و قطعات، مانند تركها، بریدگیها و نواحی مكهای سطحی، مورد استفاده قرار میگیرد. این روش تقریباً برای هر نوع ماده و در هر اندازهای، چه بزرگ با شكل پیچیده و چه ساده، قابل استفاده است و معمولاً برای بازرسی تولیدات ریختگی و كار شده فلزات آهنی و غیرآهنی، آلیاژها، سرامیكها، ظروف شیشهای و مواد پلیمر به كار میرود.
بازرسی فنی (Industrial Inspection )
بازرسین فنی معمولاً مسئولیت بازرسی تجهیزات مكانیكی، الكتریكی و … را با انجام مراحل مختلف بعهده میگیرند. بعضی از این مراحل عبارتند از:
بازرسی و كنترل براساس نقشههای ساخت، بررسی و تنظیم برنامههای نظارت بر ساخت و تولید محصول، پیگیری انجام تعهدات تولیدكننده، كنترل مقادیر در كیفیت مصالح و تجهیزات بكار رفته و پیشرفت كار، كنترل جوشكاری، كنترل رنگ آمیزی، كنترل حفاظت كاتدیك، مطابقت نقشههای ساخت و مونتاژ با استانداردهای مورد نظر، بازرسی از مراحل بستهبندی جهت اطمینان از استحكام لازم و در نهایت ارسال تائیدیه بازرسی كالا برای كارفرما.
آزمایش جریان گردابی (Eddy Current Testing)
اساس روشهای آزمون الكترومغناطیسی بر این است كه وقتی یك سیم پیچ حامل جریان متناوب، نزدیك مادهای تقریباً رسانا قرار داده شود، جریانهای گردابی یا ثانویه در آن ماده القا خواهد شد. جریانهای القایی، میدانی مغناطیسی ایجاد خواهند كرد كه در جهت مخالف میدان مغناطیسی اولیه اطراف سیم پیچ است. تاثیر متقابل بین میدانها موجب ایجاد یك نیروی ضد محركه الكتریكی در سیم پیچ شده و در نتیجه سبب تغییر مقدار مقاومت ظاهری سیم پیچ خواهد شد. اگر ماده از نظر ابعاد و تركیب شیمیایی یكنواخت باشد.
مقدار مقاومت ظاهری سیم پیچ كاوشگر نزدیك سطح قطعه در كلیه نقاط سطح قطعه یكسان خواهد بود، به غیر از تغییر اندكی كه نزدیك لبههای نمونه مشاهده میشود. اگر ماده ناپیوستگی داشته باشد، توزیع و مقدار جریانهای گردابی مجاور آن تغییر میكند و در نتیجه كاهشی در میدان مغناطیسی در رابطه با جریانهای گردابی به وجود میآید، بنابراین مقدار مقاومت ظاهری سیم پیچ كاوشگر تغییر خواهد كرد.
از روی تحلیل این آثار میتوان در مورد كیفیت و شرایط قطعه كار نتیجهگیری كرد. این روشها بسیار متنوع هستند و با وسیله و روش آزمون مناسب، میتوان آنها را برای آشكارسازی عیوب سطحی و زیر سطحی قطعات و تعیین ضخامت پوشش فلزات به كار برد و اطلاعاتی در زمینه مشخصات ساختاری مانند اندازه دانه بندی و شرایط عملیات حرارتی به دست آورد.همچنین میتوان خواص فیزیكی مانند رسانایی الكتریكی تراوایی مغناطیسی و سختی فیزیكی را تعیین كرد.
بازرسی به روش چشمی (Visual Testing)
بازرسی چشمی: در بیشتر اوقات، اولین مرحله در آزمون یك سازه، بازرسی چشمی است. بازرسی با چشم غیر مسلح فقط عیبهای نسبتاً بزرگی را كه به سطح قطعه راه دارند، نمایان خواهد كرد. با به كار بردن یك میكروسكوپ میتوان كارایی بازرسی چشمی را افزایش داد. مناسبترین نوع میكروسكوپ برای بازرسیهای سطح قطعه، میكروسكوپ استریو است. در این نوع بازرسیها، بزرگنمایی بسیار زیاد ضرورتی ندارد و بیشتر میكروسكوپهای كه بدین منظور در دسترس هستند، بزرگنمایی در حدود 5 تا 75 برابر دارند. بازرسی چشمی منحصر به سطح خارجی نمیشود. حساسههای بازرسی نوری، از هر نوع صلب و انعطاف پذیر، جهت بازرسی سطوح داخلی ساخته شدهاند. حتی این حساسهها را میتوان در داخل حفرهها، لولهها و كانالها قرار داد
بازرسی جوشی (Welding Inspection)
كنترل كیفیت عملیات جوشكاری از زمان تنظیم دستورالعمل تا انتهای كار (شامل مواردی نظیر تجهیزات، الكترود، پرسنل جوشكار و … ) بعهده بازرسی جوش میباشد كه در صورت مشاهده ایراد در هر مرحله از كار، با جلوگیری از روند ایجاد كار معیوب، راهكارهای بهبود كیفیت را ارائه میكند و تا نتیجه كار، مطلوب و طبق استاندارد درخواستی كارفرما، ایجاد گردد. انواع ترك از عیوبی هستند كه در صورت مشاهده باید كاملاً از سطح كار حذف شوند.
منبع :
با تشکر از وبلاگ مواد و متالورژی
www.smsm.ir
آزمونهای غیر مخرب ( Non Destructive Testing)
کلمات کلیدی : آزمونهای,غیر,مخرب,(,Non,Destructive,Testing),آزمونهای غیر مخرب ( Non Destructive Testing) , مقالات مهندسي , مهندسي مكانيك , کامپیوتر، مکانیک، برق، عمران، شیمی، پزشکی آزمونهای+غیر+مخرب+(+Non+Destructive+Testing)+
- آخرین مطالب مشاهده شده توسط کاربران :
نویسنده پست : علي
عنوان پست : آزمونهای غیر مخرب ( Non Destructive Testing)
منبع اصلی مطلب سایت :
- مطالبی جالب از علی بن ابیطالب(ع)
- فبلت Fonepad Note 6 ایسوس وارد بازار ایران شد
- فنجانی که موسیقی پخش می کند
- اشعار شب قدر
- آشنایی با گجت های تحسینبرانگیز
- قانون سینوسها
- دسر شکلاتی با کاکائو
- درخواست پیشنهاد یا RFQ چیست؟ Request for Quotation
- سوسك جاسوس، یك ربات زنده!
- ترکهای سطوح بتنی Cracks in concrete surfaces
- تلفن همراه مخصوص نابینایان
- چرا خداوند از حق الناس نمی گذرد؟
- موسی که با تنفس کار می کند
- سیستم های کنترل هوشمند موتورخانه
- واقعیترین ربات انساننما رونمایی شد
- مغز انسان و آینده صنعت رباتیك
- Subnetting به زبان ساده
- ترکهای سطوح بتنی Cracks in concrete surfaces
- درخواست پیشنهاد یا RFQ چیست؟ Request for Quotation
- رباتها ناجی بیماران اختلال اعصاب
- ثبت پتنت جدید اپل
- دو ابزار هوشمند به درد بخور
- سوسك جاسوس، یك ربات زنده!
- اهمیت پرورش گیاهان دارویی در فضای سبز شهری
- مروری بر پیشینه آلودگی هوا، منابع و راههای پیشگیری
- عیوب ناشی از ماسه داغ در خطوط قالبگیری با ماسه تر
- خوردگی فلزات در تجهیزات و ماشین آلات صنعتی و روش های جلوگیری از آن
- آشنایی با شبكههای لرزهنگاری مركز لرزهنگاری كشوری + اطلاعات آنلاین زمین لرزه های ایران
- آشنایی با انواع پلیمرها، كاربرد و خواص آنها
- فارس من| اهمیت شبکه ملی اطلاعات در افزایش کیفیت و قیمت پایین خدمات است
- اختتامیه یازدهمین جشنواره بینالمللی فارابی برگزار شد/ 4 توصیه وزیر علوم به متخصصان علوم انسانی و اسلامی
- تلفن همراه مخصوص نابینایان
- فنجانی که موسیقی پخش می کند
- موسی که با تنفس کار می کند
- معرفی یک باگ جدید در ویندوز 7
- نحوه گرفتن عکس پانوراما
- عینک متاپرو چیست؟
- گوشی های هوشمند جدید
- لپ تاپ لمسی با نمایشگر معلق به بازار وارد شد
- گوشی Elife E7 mini
- آشنایی با گجت های تحسینبرانگیز
- فبلت Fonepad Note 6 ایسوس وارد بازار ایران شد
- علت فروش ضعیف LG G2 چیست ؟
- چگونه امنیت مودم ها را افزایش دهیم ؟
- زندگینامه نیکی کریمی
- تزیین هندوانه شب یلدا
- خواص اناردربهبود بیماری ها
- دسر شکلاتی با کاکائو
- قانون سینوسها
- تازههایی از دنیای دانش و فناوری
- نامگذاری و شناسایی گریس
- فنجانی که موسیقی پخش می کند
- قانون سینوسها
- دسر شکلاتی با کاکائو
- فبلت Fonepad Note 6 ایسوس وارد بازار ایران شد
- علت فروش ضعیف LG G2 چیست ؟
- Subnetting به زبان ساده
- موسی که با تنفس کار می کند
- سوسك جاسوس، یك ربات زنده!
- درخواست پیشنهاد یا RFQ چیست؟ Request for Quotation
- چرا خداوند از حق الناس نمی گذرد؟
- معرفی یک باگ جدید در ویندوز 7
- اشعار شب قدر
- مغز انسان و آینده صنعت رباتیك
- تلفن همراه مخصوص نابینایان
- ترکهای سطوح بتنی Cracks in concrete surfaces
- دو ابزار هوشمند به درد بخور
- شب قدر
- Captain Shahbazi’s international campaign and his stat...
برترین های ماه
- تازههایی از دنیای دانش و فناوری
- نامگذاری و شناسایی گریس
- دعاى روز نهم ماه مبارك رمضان
- نکات مثبت و منفی نوشیدن قهوه
- آشنایی با مدار فلوتاسیون در کارخانه کانه آرایی چادرملو
- سیستم های کنترل هوشمند موتورخانه
- Subnetting به زبان ساده
- مدیریت بازیافت خودرو
- زندگینامه نیکی کریمی
- درخواست پیشنهاد یا RFQ چیست؟ Request for Quotation
- قانون سینوسها
- بیانیه و کمپین جهاني كاپيتان هوشنگ شهبازی
- اشعار شب قدر
- Captain Shahbazi’s international campaign and his stat...